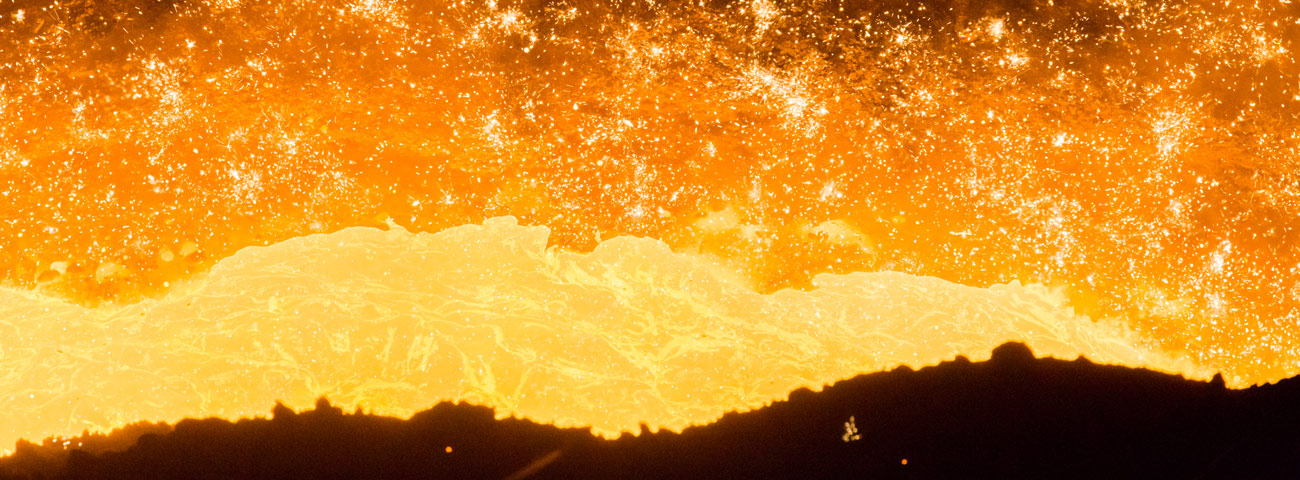
In the near future, a cell for semi-solid die-casting, also known as Rheocasting, will be installed at the EDiM plant in Quero. Rheocasting is a technology that was developed from the consolidated production process of high-pressure die-casting, retaining its advantages and adding others. In traditional die-casting, liquid aluminium is injected at high speeds and pressures into a steel mould. This creates an aluminium casting that contains the end products to be produced. Once the casting has been extracted, the mould is closed and is ready for a new production cycle. It can be reused many times, with economic benefits and leaves a smaller environmental footprint than disposable moulds. These features make die-casting an ideal solution for mass production with high process repeatability. The automotive sector, which is EDiM’s reference sector, hosts numerous applications for this production technology. Dozens of aluminium components are installed in each car, and these form EDiM’s core business. They include steering boxes as well as the parts that make up the engine, gearbox, suspension, transmission etc. Rheocasting applications further extend the portfolio of products that can be produced for the automotive sector and for other sectors such as telecommunications.
SO WHAT ARE THE BENEFITS OF RHEOCASTING? PRODUCTION SPEED AND REPEATABILITY, IMPROVED WELDABILITY, OPTIMISED HEAT EXCHANGE, IMPROVED MECHANICAL PROPERTIES AND FATIGUE RESISTANCE, LOWER WEIGHT.
Compared to other production technologies such as chill casting or sand casting, traditional die-casting already offers significantly lower production times for individual parts while ensuring high process repeatability. Rheocasting exploits these characteristics and enhances them: for example, compared to those used for traditional die-casting, Rheocasting requires slightly smaller presses, further reducing the cycle time and increasing the production rate.
Moreover, Rheocasting also brings its own benefits, mainly due to the special aluminium alloy treatment, which is the heart of this technology. In fact, a mechanical treatment is applied to the aluminium alloy. It is a sort of “blending” carried out immediately before pouring the alloy into the mould, which transforms it from a completely liquid state to a more pasty, semi-solid state. This material is then injected into the mould much more slowly than liquid aluminium, filling it in an even, linear manner without trapping any air to create a casting that is practically free from defects and cavities. This has a huge impact on the properties of the finished product, for example in terms of weldability. Castings obtained through conventional die-casting are complex to weld to each other because they are porous inside, like a sponge, a characteristic that becomes more evident with thicker workpieces. Any air inside the casting creates bubbles during welding, which compromise the process. As Rheocasting does not trap air in the mould, it avoids this problem and allows perfects welds.
In addition to weldability, it also improves the heat exchange coefficient of the finished part, giving it a higher heat transfer capacity. In electric vehicles, for example, this is especially relevant because the motor and batteries naturally develop large amounts of heat. Building shields around the motor or batteries such as those offered by Rheocasting means being able to efficiently transfer the heat generated and limit the temperature rise.
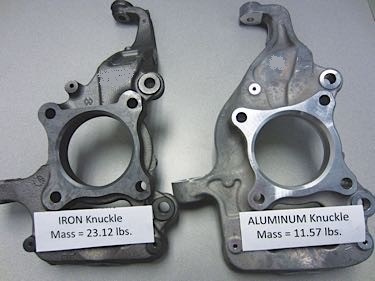
The solid, non-porous structure also ensures greater strength and resistance to deformation, making the part more durable over time and allowing the use of aluminium for components that traditionally required materials such as steel or cast iron, resulting in a finished part that weighs less. In the automotive sector, for example, this is especially relevant because making lighter vehicles reduces consumption and allows them to achieve a better environmental classification. This offers obvious benefits for vehicle manufacturers, users and the surrounding environment alike.
Despite the complicated period we are going through globally, EDiM has decided to invest in a technology that is not widely used yet in the market by acquiring Rheocasting machinery, aided by support from Bosch. To do this, we relied on a Swedish partner that holds the patent for this technology. Sweden is one of the most advanced European countries in this area, and this partner will provide us with the support needed to implement this project in the best way. At a national level, the University of Padua will follow the Rheocasting project, posting a materials engineer in the company to write a thesis on this subject. Even in a historical period like this, with the difficulties posed by a shrinking market, EDiM continues to invest in cutting-edge solutions designed to bring measurable and concrete benefits to our OEM customers.